Betti’s throwback to the start of our first transfer project
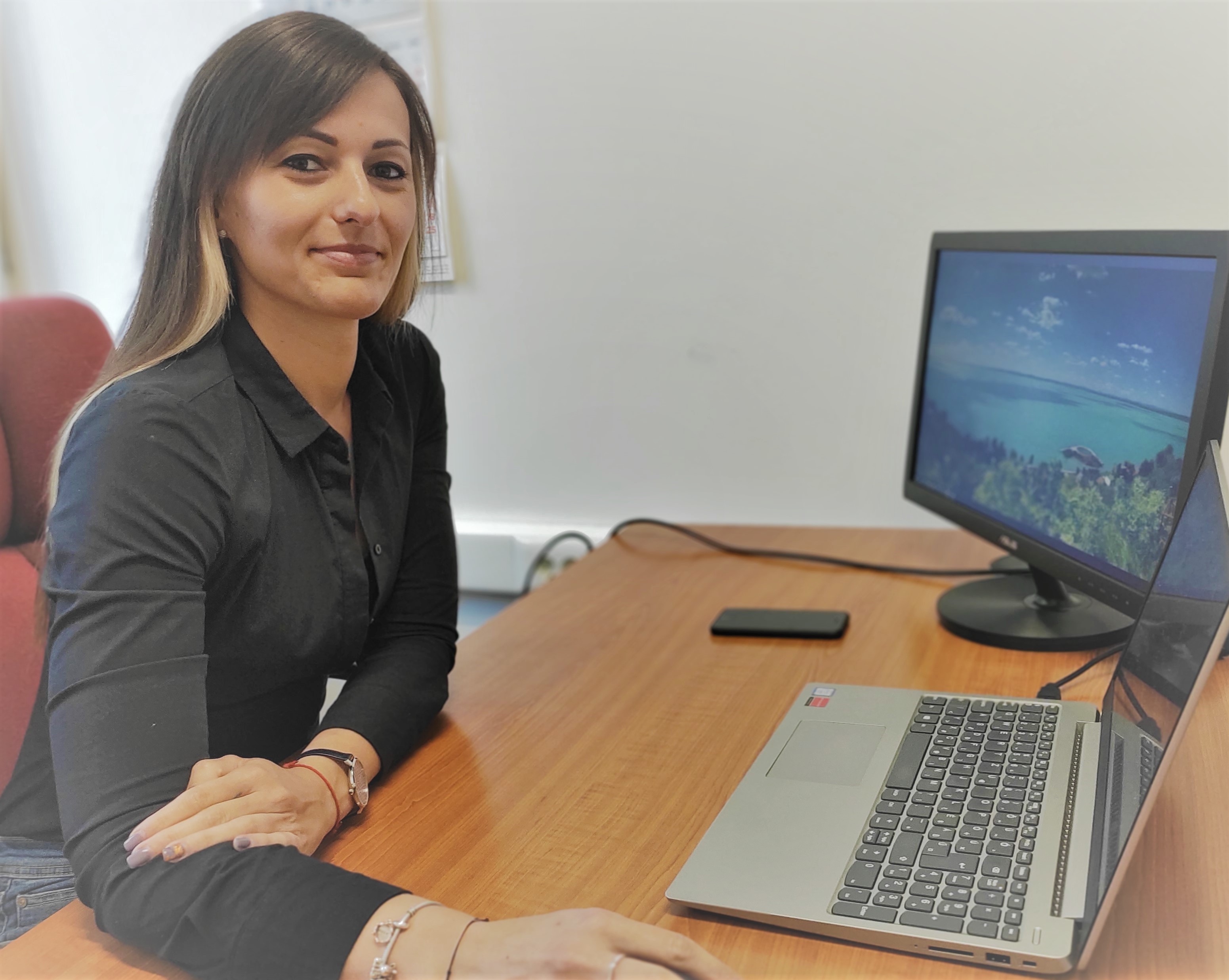
I started to work at VT ES Ltd in March 2016 where, as a buyer, I could join right away a very exciting production relocation project. The customer, mainly for cost reduction reasons, wanted to relocate an assembly unit for industrial filtration systems from one of its sites, located in Germany. The customer provided us all the available raw materials, semi-finished products, production tools and JIGs related to the project, which were delivered to our site by more than 40 24-ton trucks in almost 3 weeks. We developed a new product calculation method for the pricing of the products, which included nearly 400 types of finished goods and nearly 1000 built-in parts, as this was the first so complex raw material and finished product diversity assembly and production relocation project in the company’s life.
The announcement in Germany was followed by the depopulation of the company, as a result of which the capacity of the available indirect and direct workers was insufficient to fulfill customer orders. The fact that the German organization carried out a three-sided outsourcing parallel to several other countries not only made the situation more difficult but also created a specific form of co-operation. One day we received a phone call asking for our help to reduce the significant backlog in fulfilling customer orders, because supply capacity was already at a critically low level by then. Our job was to travel to Germany with our project team, and join the local team to fulfil customer orders while we actual train in.
The work began immediately: a week later, our team worked on its own though under supervision, and soon reached the efficiency level of the local team, and so, together we were able to catch up and close the gap between ordered and produced quantities quickly. The local management appreciated our prompt assistance. At their request, due to market pressure, the training period previously planned for 4 weeks was extended to 4 months. During this time, we worked also on weekends when required, and kept in touch with the colleagues at home, who not only helped and supported our work in Germany based on the information and instructions received, but also worked in parallel on making the transfer well prepared and smooth. The extended training time was in some respects beneficial for us as well, because only part of the products had documentation, which would have made it very difficult to start the production prompt in Székesfehérvár. Thus, with the effective help of the German colleagues, we had the opportunity to recreate most of the missing documents in these 4 months.
My main task was to become familiar with the procurement and logistic processes, as well as to get acquainted with suppliers and raw materials. The purchaser at the German Company - who managed the nearly 1,000 types of built-in parts at roughly 250 different suppliers with his long years’ experience - left the company in this transition period, which made my task to take over his job almost hopeless. Afterwards I worked on my own under the supervision of the German colleagues remaining with the company. I got purchaser access to their own system, based on which I issued orders and participated in the material supply and the organization of logistic processes. Today, I work as a deputy project manager in the project team.
During the 4 months we learned a lot of new things in a lean environment - which we taught the staff at home for years so that we can take over and maintain what we learned abroad -, and we also managed to establish a personal relationship in the field of operational cooperation. Thus, with the know-how, experience and connections gained there, we were able to implement the project more smoothly and on time in Hungary. This success was measurable also for the customer, as even after the completion of the transferred 1M € backlog, we still deliver in the expected quality on 100% OTD.